BeePlanet Factory: “Es necesario un cambio en la fabricación de los productos, y en concreto de las baterías”
El pasado 21 de mayo tuvimos la oportunidad de conocer a Beeplanet Factory, compañía que nació para contribuir a la implementación del almacenamiento sostenible de energía, utilizando baterías del vehículo eléctrico y, que recientemente acaba de lanzar su primer producto al mercado: BeeBattery® Home.
A través de una entrevista telemática con Alfonso Urrizburu, Ingeniero de Desarrollo de Producto en la empresa, descubrimos la importancia de dotar de una segunda vida a las baterías de ion-litio, cómo es este proceso y cómo incorporan la economía circular en toda su actividad.
El proyecto que estáis desarrollando es muy interesante, además es pionero en España. ¿Por qué decidisteis empezar esta idea de negocio?
Así es, es pionero en España. Hay alguna empresa más en Estados Unidos, otra en Reino Unido, y creo que una más en Bélgica, pero no mucho más.
Actualmente, nos encontramos en un estado de mercado muy incipiente porque, es verdad, la adopción del vehículo eléctrico no es masiva, aunque Nissan lanzó su primer vehículo eléctrico hace diez años. Y es ahora cuando empiezan a surgir los problemas de fin de vida en la batería del vehículo eléctrico. Por obligación legal un fabricante de automóviles tiene que reutilizar o reciclar más del 85% del peso del coche y una batería eléctrica es el 30-35% del peso total. Y si ese proceso no es rentable y si encima no hay empresas que lo puedan hacer de manera masiva, los problemas que tienen los fabricantes de automóviles en cuanto a la batería son reales. Empiezan a tener almacenes llenos de baterías. De ahí surge esta iniciativa empresarial, con vocación de liderar la solución a ese problema. Además, ser pioneros nos posiciona como “un primer actor”, lo que nos permite aprender todo lo necesario para cuando el mercado del vehículo eléctrico se asiente.
¿Qué significa la sostenibilidad para Beeplanet Factory?
Nuestro ámbito de actividad es la ingeniería y las baterías reutilizadas. Pero, para nosotros el mensaje de sostenibilidad es algo que permea toda nuestra propuesta de valor. Le queremos dar la entidad que merece y por eso estuvimos embarcados con una consultora que se dedica a temas de economía circular y sostenibilidad en un proyecto de sostenibilidad. Primero, realizamos un análisis completo, tanto de nuestros productos como de la empresa, y de ahí, extrajimos una serie de conclusiones de cómo hacer el negocio más sostenible y rentable; cómo podíamos ahorrar más emisiones de CO2 a la atmósfera o cómo podíamos conseguir una cartera de proveedores locales.
Además, la sostenibilidad cobra mucha más importancia cuando hablamos de materiales que son verdaderamente necesarios para una actividad económica, como ocurre en el caso de las baterías.
¿Podrías explicarnos la importancia de reutilizar las baterías?
El tema de la electrificación del sistema en general mediante la inclusión de energías renovables, tanto de las redes, como en el vehículo eléctrico y en el ámbito residencial implica la instalación de baterías para la gestión energética. Baterías que, en su mayor parte, no se producen aquí, en Europa. Además, no hay prácticamente minas de litio en Europa. La mayor parte de desarrollos están en Asia y Estados Unidos. En nuestro ámbito, se está fomentando una gran cadena de suministro circular, de modo que todas las baterías de litio del exterior, las reciclemos y los materiales se queden aquí. Y esperamos que en un futuro este sistema de economía circular nos permita ser “autosuficientes” en ciertas tecnologías que son necesarias.
¿Cómo es el proceso de recuperación de baterías? ¿Es sencillo?
A priori parecería un proceso bastante sencillo, pero cuando se ahonda en ello, es costoso. Es bastante intensivo en mano de obra y conocimiento porque realmente lo que hay que hacer es desmantelar el coche, y, o reutilizamos el battery pack entero, o de ahí extraemos los módulos o celdas. Cada coche tiene entre 48 y 50 módulos de baterías y, en función del equipo que nosotros hagamos, reutilizamos el batterypack entero o los módulos. Antes de esto, tenemos que saber la capacidad efectiva disponible y conlleva un proceso de testeo eléctrico y químico que hay que conocer en profundidad. A partir de ahí, hay que dotar a la batería de cierta inteligencia con una placa electrónica. Además, la seguridad es un aspecto clave en nuestro negocio, puesto que realizamos trabajo en tensión.
En resumen, el proceso requiere una forma de aprendizaje muy lenta e intensiva en capital, por eso no hay muchos profesionales que puedan dedicarse a ello.
¿Qué beneficios ofrecéis al cliente y al medioambiente con vuestros productos?
Los beneficios no cambian mucho de un producto a otro. Al final lo que hacemos es aumentar la capacidad. Ofrecemos a nuestros clientes, un equipamiento de almacenamiento de energía más barato que la competencia, un producto seguro y monitorizado.
En relación con el medioambiente, nosotros evaluamos la contribución que tienen nuestros productos al respeto del medioambiente, pero también, su impacto. Realizamos una evaluación LCA (Análisis ambiental del ciclo de vida) y según este estándar, conseguimos ahorrar más de 4200 kg de CO2 sobre un ciclo de vida completo en comparación a una batería nueva. También, tenemos un impacto virtualmente cero en cuanto al uso de materias primas y biodiversidad en los ecosistemas durante toda la vida útil del producto. No es solo no contaminar, sino también no utilizar materias primas críticas con un alto coste de extracción como puede ser el litio o el níquel.
«Un modelo energético basado en materias primas no renovables conduce a la escasez, a un sistema energético más contaminante y más caro».
¿Qué ocurre cuando se acaba la vida útil de los equipos de almacenamiento sostenible? ¿Los recicláis?
Sí, cuando planteamos nuestro modelo de negocio, lo planteamos como un círculo: desde el desmantelamiento de los fabricantes, la creación, venta y reciclaje. Cuando hablamos de reciclaje, hoy en día no tenemos la capacidad para hacerlo en nuestras instalaciones. Por eso, estamos integrados en un SCRAP (Sistema colectivo de responsabilidad ampliada del productor) y cada vez que ponemos una batería en el mercado pagamos una tasa, al final de la vida útil de esa batería, nuestro partner la recoge y se recicla. Existen diferentes métodos, hidrometalurgia, pirometalurgia etc., de modo que se puedan extraer aquellos materiales que son críticos, como por ejemplo, el litio. Y con ese litio, se pueden volver a generar baterías de primera vida para un vehículo eléctrico.
¿Cómo ha sido la acogida de vuestros productos en el mercado?
Acabamos de lanzar el producto BeeBattery® Home, focalizado en el ámbito residencial y, la verdad, está teniendo buena acogida. El otro día hicimos un webinar porque teníamos dos instalaciones previstas, tenemos otra instalada en Barcelona, otra en Valladolid y alguna nueva que vamos a hacer en Portugal. Está teniendo mucha acogida, tanto la empresa porque es algo novedoso, como la batería porque tiene un precio más bajo que sus homólogas.
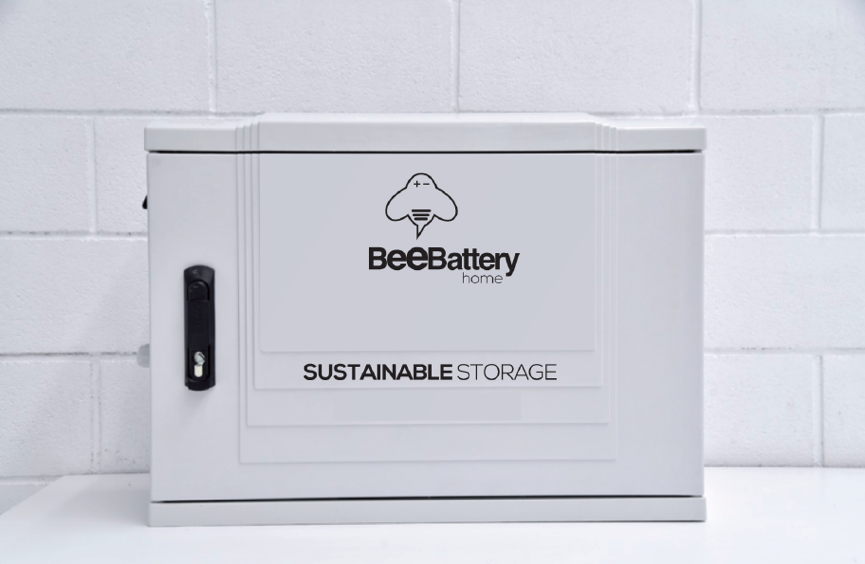
En BeePlanet Factory realizáis lo que se acuña como “minería urbana” que consiste en recuperar los minerales y metales de productos desechados en vez de extraer los recursos naturales de las minas ¿Por qué pensáis que es necesario este cambio de modelo?
Nosotros pensamos que tiene que haber un cambio de modelo en la fabricación de los productos, y en concreto de las baterías. Al final un modelo energético basado en materias primas no renovables conduce a la escasez, a un sistema energético más contaminante y más caro. Lo que proporciona un sistema más renovable, aparte de no depender del exterior a nivel estratégico, es tener un sistema más barato porque en el mercado eléctrico la renovable y la fotovoltaica entran a valor cero. Sin embargo, cabe destacar que, este modelo renovable no tiene sentido sin almacenamiento. En un ciclo combinado o en una central de carbón pueden regular perfectamente su producción “o metemos menos en el horno o metemos más”. Pero, la solar y la eólica necesitan el almacenamiento para poder ser gestionables. Y es esta capacidad de gestión la que va a permitir la adopción de un modelo más sostenible.
¿Imagináis un futuro en el que todos los aparatos eléctricos y electrónicos estén fabricados con elementos recuperados?
Sí, al final iremos tendiendo hacia ese modelo, porque cada vez va a haber más sanciones o más promoción por parte de los gobiernos, para mantener los materiales aquí. Además, cada vez es más posible: los procesos de recuperación son más precisos, más avanzados. Por otro lado, cada vez queremos productos más sostenibles y provinientes de una cadena de suministro más local o nacional.
¿Qué nuevos proyectos estáis desarrollando?
Al llevar solamente un año y medio de actividad, todo: la propia empresa y los productos de la gama de más alta capacidad. Además, estamos realizando desarrollos propios sobre el control de la batería y de la instalación, lo que se llama BMS (Battery Management System) y EMS (Energy Management System) y que permite gobernar la batería y los sistemas de monitorización remota. Este sistema prevé, por ejemplo, que mañana va a hacer nublado y por tanto nos permite cargar la batería por la noche a un precio más barato para al día siguiente disponer de energía. También, investigamos a nivel de testeo. Es muy interesante para nosotros conocer de manera precisa y rápida cuánta vida útil les queda a nuestros módulos y baterías.
Por último, ¿cuáles son los retos a los que os enfrentáis?
El producto supone un reto en sí mismo. Más allá del propio negocio de modelo circular, la puesta en el mercado de los productos también es circular porque ofrecemos el reemplazo de módulos, una vez que se le gasta la energía al cabo de diez años. Tenemos el desafío de sustituirlos, sin sustituir la caja, la electrónica, los componentes. Hacer casi un producto para siempre. Esto permite que sea prácticamente un producto circular dentro de un modelo circular.